The 3TER® hollow auger pile is a new generation continuous flight auger pile, operated using a specific work group to ensure a better quality of concreting when the auger train is raised. This improvement is achieved by the action of a rotating telescopic dip tube (TER) at the bottom of the auger, equipped with 2 lateral vents in the lower part allowing immediate concreting as soon as it comes out. These 2 vents remain permanently immersed in fresh concrete, ensuring a better concrete quality than the type 2 hollow auger. The process always makes it possible to maintain the tightness of the concrete pipe during the drilling phase and to check pipe outlet under all drilling and concreting conditions.
In order to improve the quality of the pile concreting, the telescopic tube is controlled by the rotation of the auger, which ensures perfect homogeneity of the concreting during the construction of the pile. This rotation of the vents is also a way to improve ground-concrete contact along the drum and the bearing capacity of the 3TER® pile tip.
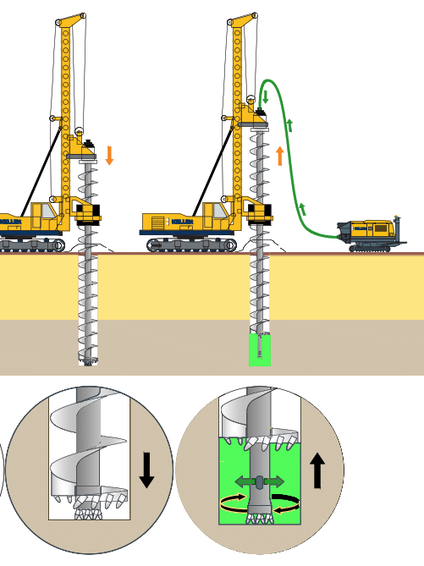
Common uses
Process
Set up the drill so that the tool axis rests precisely on the right side of the reference mark shown on the ground. Before retracting the telescopic tube into the auger, a visual inspection of the clearance of the vents is carried out to check they are free from any concrete.
Drilling the pile: When the tool is lowered, the rotation speed and pull-down are adapted to the nature and compactness of the soil or rock encountered and are displayed on real-time graphs. These drilling parameters measured make it possible to verify the anchor lengths defined by the calculations and validated by the preliminary drilling tests. The verticality of the auger is monitored from markers (metal rods) planted in the ground and placed on either side of the auger on the 2 perpendicular planes.
Concreting the pile: after drilling to the final depth, the material (mortar or concrete) of suitable consistency is pumped in by raising the tool while keeping the concrete tube in contact with the bottom of the borehole. The concreting is then continued with the rotating telescope fully extended by raising the auger and the dip tube extended to platform level. The concrete vents are located at least 80 cm below the upper level of the concrete. The concrete pressure and the ascent rate are adapted by the operator to always obtain an over-consumption of concrete in relation to the theoretical volume. The minimum concrete pressure is 10 kPa (except at the end of the concreting process).